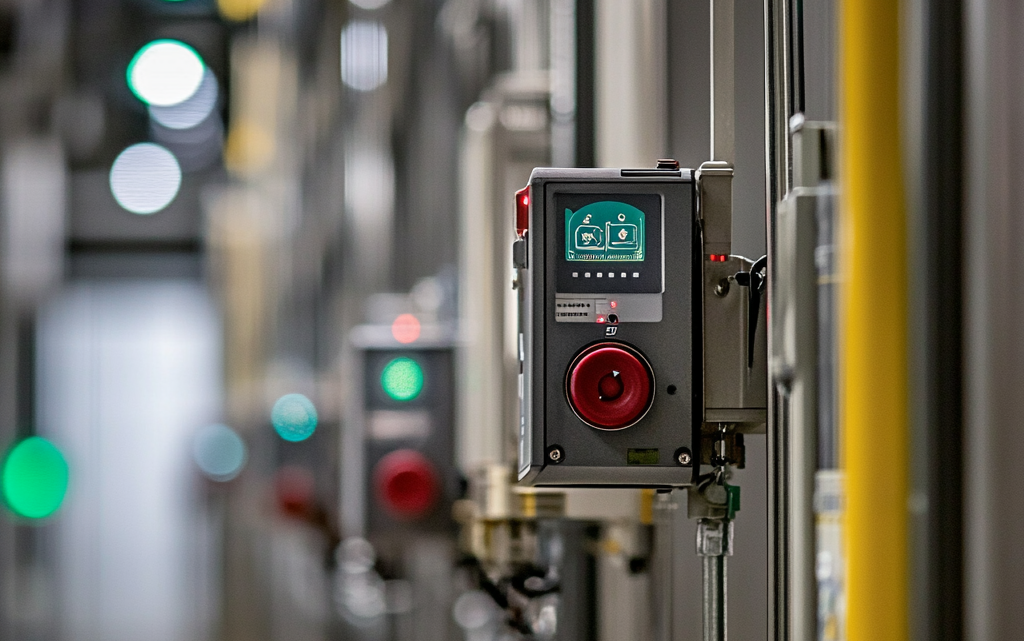
Automation of the transportation process: how robots and AI improve warehouse operations
Process automation in warehouse logistics has long ceased to be just a trend and has become an integral part of modern business practices. The introduction of robots and artificial intelligence (AI) is radically changing not only the way warehouses operate, but also the very nature of logistics. Gone are the days when warehouses were places where people manually moved goods, reported inventory, and packed packages. Today, labor-intensive and erroneous processes have been replaced by high-tech solutions that can work without fatigue and with maximum precision.
Robots in warehouses: the key to improving speed and accuracy
Implementation robots in warehouses has become a real revolution in logistics. These devices provide fast and precise handling of goods and materials, which significantly speeds up the entire processing process. Robots can efficiently sort products, move them around the warehouse, and perform routine tasks such as packaging and labeling. This reduces human errors and improves overall productivity.
Additionally, the use of robots allows warehouse operators to focus on more complex tasks such as planning and quality control. Robots can work 24/7, which makes them indispensable for warehouses where high speed processing of large volumes of goods is required. Even under conditions of increased load, robots ensure stable operation without interruptions, which is especially important in the context of modern logistics requirements.
Artificial intelligence in warehouse process management
Artificial intelligence (AI) in warehouse management can significantly improve forecasting needs, route optimization and inventory. AI analyzes a huge amount of data in real time and, based on this data, makes predictions about what goods and in what volume will be in demand in the future. This approach avoids both stockouts and overproduction of goods in the warehouse, which reduces storage costs and improves overall operational efficiency.
- Demand Forecasting: AI can analyze historical data and current trends to predict which products will be most in demand in the near future. This allows you to prepare in advance for a large flow of orders and optimize purchases.
- Optimization of routes and processes: AI helps optimize routes for robots and warehouse employees, minimizing the time it takes to move goods and reducing the number of errors.
- Inventory management: AI allows, based on collected data, to automatically recalculate inventories and prepare orders for replenishment, minimizing the possibility of human error in accounting.
Usage artificial intelligence makes it possible to improve not only the speed of work, but also its accuracy. AI constantly learns and adapts to new conditions, making the system smarter every day. This is especially useful in times of changing market trends and seasonal demand fluctuations.
Automation of packaging and sorting: increasing efficiency
One of the most important aspects of warehouse process automation is packaging and sorting of goods. Modern automated systems are capable of not only quickly packing goods, but also doing it with high accuracy, observing all the necessary parameters. Automated machines can sort products into categories, direct them to the right sections, and quickly create orders for shipment.
Packaging automation allows you to get rid of errors, such as incorrect choice of packaging or damage to the product during the packaging process. In some cases, with the help of technology 3D scanning and visual inspection, systems can determine how well a product meets its stated specifications and, if necessary, redirect it for inspection. Such systems become indispensable in warehouses with a large number of goods, where human labor cannot cope with the high load.
In addition, packaging automation allows reduce the cost of packaging materials and reduce the amount of waste, which has a positive effect on the economic efficiency of the business. This allows companies to offer better deals to customers, reducing shipping costs and improving competitiveness.
Integrating robotics with traditional warehouse systems
The introduction of robots and AI does not exclude the use traditional warehouse systemssuch as inventory management And warehouse management systems (WMS). On the contrary, new technologies are actively integrated with existing solutions, which makes it possible to create a single effective management system. Robots and AI do not replace traditional work methods, but make them more efficient, reducing the time required to complete routine tasks.
For successful integration, many factors must be taken into account, such as coordination with logistics programs, the ability of robots to work with different types of goods and real-time system support. Integration of modern technologies with already operating systems allows reduce costs for implementing new solutions and accelerate the transition to automated processes.
Thus, robotics and AI are becoming an integral part of traditional warehouse logistics, making it more flexible and adaptable to change. Companies that successfully integrate these solutions gain significant competitive advantages by improving service quality and reducing lead times.
Robots and AI in inventory management: minimizing errors and losses
One of the main problems of traditional logistics is inventory management And inventory, which have always been subject to human error. Manual inventory of goods, especially in large warehouses, often leads to errors, omissions and losses. Robots and AI are radically changing this situation, providing automatic updating and accurate inventory accounting.
Robots can be equipped with sensors and cameras that allow them to scan barcodes and QR codes of products, and AI analyzes this data to determine accurate stock levels. This allows not only to exclude inventory errors, but also warn in advance about possible shortcomings or surpluses of goods. In addition, AI-powered systems can automatically order the necessary products, based on demand analysis, which significantly reduces the likelihood of product shortages and surpluses.
Along with this, AI systems can optimize not only the storage of goods, but also their distribution throughout the warehouse, which allows minimize time for search and transportation. This approach enables companies to operate more flexibly, quickly adapt to changes in demand and improve overall operational efficiency.
Automation of the processes of transportation and storage of goods through implementation robots And artificial intelligence changes not only the work of the warehouse, but also the very nature of logistics. These technologies can significantly increase speed, accuracy And efficiency work, reducing costs and minimizing errors. The introduction of new solutions, such as automation of packaging, sorting and inventory, is helping companies cope with increasing product volumes and delivery time requirements.
Every year these technologies become more accessible and adapted for use in warehouses of various sizes. Companies that implement these solutions gain significant benefits by reducing costs and increasing competitiveness. However, it is important to note that successfully integrating robots and AI into traditional systems requires highly skilled specialists and additional investment, which can be a challenge for some businesses.
However, the future of warehouse logistics inevitably involves the use of advanced technologies. The introduction of robots and artificial intelligence makes it possible to increase flexibility And adaptability warehouse systems, making them more resistant to changes in market conditions and customer requirements. In the coming years, we can expect even greater technological developments, leading to further process improvements and even greater quality of service.
Automation reduces the need for labor, speeds up order processing and minimizes errors, which helps reduce labor, storage and transportation costs.
The main challenges are the high initial investment, the need for staff training and the integration of new technologies with existing systems.